Fiber Laser Cutting are ubiquitous in today’s world. Because of the various wavelengths they can produce, Fiber Laser (s) are widely used in industrial environments to perform cutting, marking, welding, cleaning, texturing, drilling, and a variety of other tasks. They’re also used in fields like telecommunications and medicine.
Table of content
To guide light, fiber lasers cutting use an optical fiber cable made of silica glass. Because the resulting laser beam is straighter and smaller than with other types of lasers, it is more precise. They also have a small footprint, high electrical efficiency, minimal maintenance, and low operating costs.
When Did the Fiber Laser First Appear?
In 1961, Elias Snitzer invented the fiber laser, which he demonstrated in 1963. However, serious commercial applications did not emerge until the 1990s.
What was the hold-up? The main reason for this was that fiber laser technology was still in its early stages. Fiber lasers cutting, for example, can only emit a few tens of milliwatts, whereas most applications require at least 20 watts. There was also no way to generate high-quality pump light because laser diodes did not perform as well as they do now.
Here are some pivotal moments in the history of fiber laser technology, dating back to 1917, when Albert Einstein laid the groundwork. Stimulated emissions are discovered in 1917.
- 1957 – Gordon develops the theoretical framework for the laser.
- The first laser, a ruby laser, is built in 1960.
- Continuous-wave laser beams are created for the first time in 1960.
- The term “fiber optics” is coined in 1960.
- Optical modes in glass fibers are invented in 1961.
- Q-switching, a technique for producing pulsed laser beams, is demonstrated in 1962.
- The first fiber laser is demonstrated in 1963.
- 1964 – A method for removing impurities from glass fibers and thus limiting light loss is discovered.
- The first double-clad fiber laser is demonstrated in 1988.
- 1990 – A 4W erbium-doped fiber laser breaks the watt barrier.
- The single-mode silica fiber laser and amplifier is invented in 2004.
Today, significant advances in fiber laser technology are still being made, making it more efficient, powerful, and accessible. Some of the most promising applications are laser cleaning and laser texturing, which can replace polluting technologies and contribute to a greener world.
What Are the Different Types of Fiber Lasers Cutting?
In general, fiber lasers cutting can be classified according to the following criteria:
Fiber lasers differ depending on the material with which the laser source is mixed. Ytterbium-doped fiber lasers, thulium-doped fiber lasers, and erbium-doped fiber lasers are a few examples. Because they produce different wavelengths, all of these lasers are used for different applications.
Today, significant advances in fiber laser technology are still being made, making it more efficient, powerful, and accessible. Some of the most promising applications are laser cleaning and laser texturing, which can replace polluting technologies and contribute to a greener world.
The size of the core (where light travels) in an optical fiber is referred to as its mode. Single -mode fiber lasers and multi-mode fiber lasers are the two types of modes. this kind of lasers have a smaller core diameter, typically between 8 and 9 micrometers, whereas multi-mode lasers have a larger core diameter, typically between 50 and 100 micrometers.
Single- mode lasers, on average, transmit laser light more efficiently and with higher beam quality. Fiber lasers can be classified in a variety of ways, but the ones listed here are the most common.
What Is the Distinction Between Fiber and CO2 Lasers?
The primary distinction between fiber and CO2 lasers is the source from which the laser beam is generated. The laser source in fiber lasers cutting is silica glass mixed with a rare-earth element. This in CO2 lasers is a gas mixture that includes carbon dioxide. Fiber lasers are classified as solid-state lasers due to the state of their source, whereas CO2 lasers are classified as gas-state lasers.
Different wavelengths are also produced by these laser sources. Shorter wavelengths are produced by fiber lasers, for example, with some examples ranging between 780 nm and 2200 nm.
CO2 lasers, on the other hand, produce longer wavelengths, typically ranging between 9,600 and 10,600 nm. Because of their different wavelengths, they are used for a variety of applications. 1064 nm fiber lasers, for example, are commonly used in metal processing applications.
Laser cutting is an obvious exception, where CO2 lasers are frequently used to cut metals. CO2 lasers also have a favorable reaction with organic materials. If you’re torn between the two, check out our post on deciding between a CO2 and a fiber laser.

What exactly is a Fiber Laser Cutting Machine?
When a fiber laser system is engineered into a ready-to-use solution, that solution is referred to as a fiber laser machine. The OEM laser system is the tool that performs the operation, whereas the laser machine is the framework within which the tool is integrated.
Laser machines can ensure the following:
By providing laser safety and fume extraction, workers are completely safe. Mechanical components are used to automate operations or to make the operator’s job easier. The laser process has been fine-tuned for a particular operation. The fiber laser machine depicted here, for example, includes a rotary table, a rotary indexer, a Class-1 laser safety enclosure, a fume extractor, a vision camera, and an HMI.
How Long Can a Fiber Laser Cutting Be Used?
According to most online sources, fiber laser cutting has a lifespan of 100,000 hours, whereas CO2 lasers have a lifespan of 30,000 hours. This isn’t entirely correct. These figures refer to a value known as “mean time between failures” (MTBF), which varies between fiber lasers. In reality, different numbers will be displayed for different types of fiber lasers.
The MTBF of a laser measures its dependability by indicating how many hours the laser is expected to operate before failing. It is calculated by running multiple laser units through their paces and then dividing the total number of operational hours by the total number of failures.
Although this value does not precisely indicate how long a fiber laser can last, it does provide a good indication of the laser’s dependability. If you’re looking for the exact lifespan of a fiber laser, you’ll be disappointed because there isn’t one. In reality, fiber laser cutting can fail at critical points during their lifetime.
Here’s what you need to know if your laser fails at any of these points:
Early failures are likely if a fiber laser suffers from fabrication flaws and You should have a purchase guarantee that covers fabrication errors so that the laser can be replaced at no cost.
Normal life: Once you’ve passed the first critical period of early life, the MTBF value gives you a good idea of how likely your laser is to fail. A high MTBF is a good indicator that everything will go well, but it is not a guarantee. You can prepare for failures in everyday life in a variety of ways, including having a spare laser on hand, renting a laser while yours is being repaired, or having a long-term purchase guarantee.
End-of-life: When fiber lasers are nearing the end of their useful life, the chances of failure skyrocket. Even so, a high-quality industrial laser can frequently operate well beyond its MTBF.
What Is the Function of a Fiber Laser Cutting (And What Are Its Components)?
Pump light from laser diodes is used to power fiber lasers. These diodes emit light, which is transmitted through the fiber-optic cable. The optical components in the cable are then used to generate and amplify a specific wavelength. Finally, the laser beam is formed and released.
This is how each component is used to complete this operation.
Step 1: Light is Produced by Laser Diodes
Laser diodes convert electricity into photons, or light, which are then pumped into the fiber-optic cable. As a result, they are also referred to as the “pump source.”
Diodes generate light by charging two semiconductors differently:
The first is positively charged, which means it requires an extra electron. The second is negatively charged, indicating that it has an extra electron, also known as a free electron.
When positive and negative charges collide, they attempt to combine. However, in order to do so, the free electron must be released as a photon. The number of photons rapidly increases as current flows through the semiconductors.
The light that results is pumped into the fiber-optic cable and used to generate the laser beam.
Step 2: The Pump Light Is Guided Throughout the Fiber-Optic Cable
Light travels in all directions in nature. Fiber-optic cables use two basic components to focus light in a single direction and produce a laser beam: the fiber core and the cladding.
Light travels through the core. It is made of silica glass and contains the only rare-earth element in the cable. The material that surrounds the core is known as the cladding. When light strikes the cladding, it is reflected back into the core. This is due to the cladding’s total internal reflection.
Because the cladding has a lower refractive index than the core, total internal reflection occurs. Nature exhibits similar effects. Submerged objects, for example, appear deformed when viewed from above. This is due to the fact that as light travels from air to water, it encounters a different refractive index and changes direction.
The same holds true when light travels from the core to the cladding, with the exception that the change in direction causes a reflection. Without the cladding, light would escape from the core in all directions.
However, due to the refractive index of the cladding, light remains in the core and continues its path.
List of laser cutting machines available in the company
Step 3: Light in the Laser Cavity is Amplified
Pump light eventually enters the laser cavity as it travels through the fiber-optic cable—a small region of the cable where only light of a specific wavelength is produced. The fiber is “doped” in this region, according to physical engineers, because it has been mixed with a rare-earth element.
When particles from the doped fiber interact with light, their electrons gain energy. When they revert to their fundamental state, they emit energy in the form of photons or light. These phenomena are referred to as “electron excitation” and “electron relaxation” by physical engineers.
The laser cavity also serves as a resonator, allowing light to bounce back and forth between what are known as “fiber Bragg gratings.” This results in “Light Amplification by Stimulated Emission of Radiation,” abbreviated as LASER. Simply put, this is where the laser beam is created.
Bragg gratings are classified into two types:
The first is a mirror that reflects light back into the cavity.
The second acts as a selective mirror, allowing some light to exit the cavity while reflecting the remainder back into it.
When photons collide with other excited particles, these particles also emit photons; because the Bragg gratings reflect photons back into the cavity, and more pump light is sent into the cavity, an exponential number of photons are released.
Laser light is produced as a result of this stimulated emission of radiation.
Step 4: Produce Laser Light of a Specific Wavelength
The wavelength produced by the doped fiber varies depending on the laser cavity’s doping element. This is critical because different wavelengths are used for various applications. Erbium, ytterbium, neodymium, thulium, and other elements could be used as doping elements. Ytterbium-doped fiber lasers, for example, have a wavelength of 1064 nm and are used for laser marking and cleaning.
Because specific particles emit specific photons, different doping elements produce different wavelengths. As a result, all photons produced in the laser cavity have the same wavelength. This explains why each type of fiber laser produces a single wavelength and only one wavelength.
You may be interested in the page of the laser cutting machine.
Step 5: Shape and Release the Laser Beam
Because of the light guiding properties of the fiber, photons exiting the resonant cavity form a laser beam that is extremely well collimated (or straight). In fact, it is overly collimated for the majority of laser applications. Different components, such as lenses and beam expanders, can be used to shape the laser beam.
Fiber laser cutting, for example, has a 254 mm focal length lens for laser applications that dig into the material (i.e., laser engraving and laser texturing). This is due to their short focal length, which allows us to focus more energy onto an area for more aggressive laser ablation.
Other types of lenses offer different benefits, which is why experts carefully select them when optimizing a laser for a specific application.
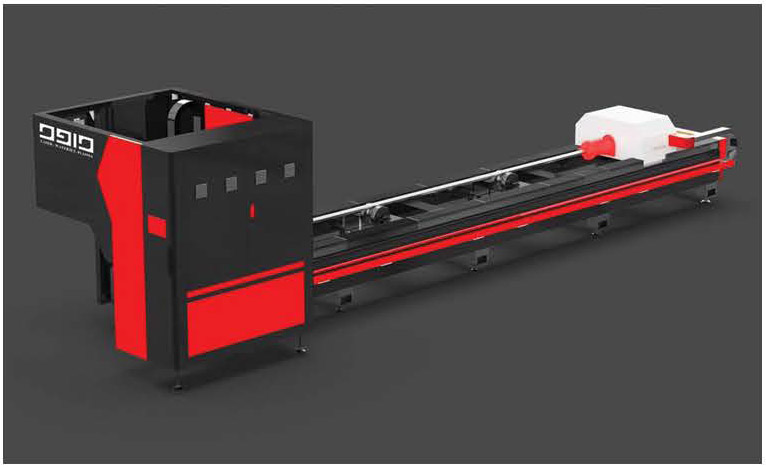
What Do the Laser Parameters Mean?
The parameters of all lasers and laser applications are not the same. Different ones, for example, must be adjusted for laser cutting and laser marking. Some parameters, on the other hand, are common to all types of fiber lasers. Here are the ones you’re most likely to come across.
A fiber laser’s wavelength corresponds to the level of electromagnetic radiation produced by the laser light. Fiber lasers typically produce wavelengths in the infrared spectrum that are invisible to the human eye, ranging from 780 nm to 2200 nm. Because this wavelength range of infrared light reacts well with metals, rubber, and plastics, it is useful for a wide range of materials processing applications.
Some fiber lasers, such as green lasers, emit visible light that reacts well with soft materials like gold, copper, silicone, and soft glass. Green fiber laser cutting is also used in holography, therapy, and surgery, to name a few applications.
You may be interested in the Press Bark page.
Operation Mode in Fiber Lasers Cutting Machine
The mode of operation refers to how the laser beam is released. Fiber lasers typically operate in one of two modes: continuous-wave or pulsed. A continuous, uninterrupted laser beam is released in the continuous-wave operation mode, which is ideal for applications such as laser welding and laser cutting.
Short pulses are released at a predetermined repetition rate in the pulsed operation mode. Pulsed laser beams have higher peak powers and are best suited for laser engraving and cleaning. The following parameters are included in this mode:
Pulse Energy: The number of millijoules contained in each pulse is referred to as the pulse energy. Each pulse typically contains 1 mJ of energy.
Pulse Duration: The pulse duration, also known as pulse length and pulse width, is the time it takes for each pulse to complete. Shorter pulses concentrate the same energy in less time and thus achieve higher peak powers. The duration of a pulse can be measured in microseconds, nanoseconds, picoseconds, or femtoseconds.
The number of pulses released per second is referred to as the pulse repetition rate. It is also referred to as the pulse frequency, which is measured in kHz. A frequency of 100 kHz corresponds to 100,000 pulses per second.
Power
The laser power is the amount of energy that the laser can produce in one second. It is also referred to as “average power” and “output power.” Pulsed lasers may also show a peak power, which is a separate parameter.
The peak power is the maximum amount of energy that a single pulse can produce. A 100W pulsed fiber laser, for example, can easily reach 10,000W of peak power. This is because, unlike continuous-wave lasers, pulsed lasers do not distribute energy evenly over time.
Beam Characteristics
The beam quality describes how close the beam is to a Gaussian beam. This is important in real-world applications because it indicates how well focused the laser beam is.
A perfect beam quality is expressed mathematically as M2=1. Well-focused laser beams concentrate more energy in a smaller area. High-quality laser beams are required for applications such as laser engraving and laser cleaning, whereas lower beam qualities may be more appropriate for applications such as laser welding where ablation is not desired.
To receive advice on choosing the best device depending on the needs of your business, contact our partners in the Davoud Industrial Lasers Group.
Fiber laser cutting board may be attractive to you.
The metal laser cutting board may be attractive to you.
You may be interested in the page of the laser welding machine.
One of the best laser cutting machines in Iran is the DA-E 3015 laser cutting machine of Daoud company.
تعداد نظرات در انتظار تایید: 1